- What to consider before installation
- General information regarding liability and warranty
- General information about materials and quality standards
- Lifetime AfterCare maintenance program
- Cancellation terms and payment
- After PPF installation
What to consider before installation
Before bringing your car to Restyling Pointille, we have created a detailed guide covering all possible general and specific situations that would be important for customers to know to avoid later surprises. If you are uncertain about the need for additional protection, we recommend checking out New Car Protection Guide.
1. Essentially, our provided prices or estimates always remain unchanged. Factors that may affect the price include force majeure situations on the installation site/customer side, conditions that the customer was unaware of/did not know in advance on both sides: the customer and Restyling Point. Example situations:
1.1. We recommend that ceramic coatings be polished off as they affect the durability of the PPF film.
1.2. Often, customers are unaware of the history of their cars and the existence of an existing ceramic coating on their vehicle. This is entirely normal. When a car is taken in for work, during the wash, if we notice a ceramic coating installed on the car, we inform the customer of the risk that if the areas to be coated are not polished, it may affect the durability of the PPF protective film due to inadequate adhesion. The cost of polishing is calculated on a case-by-case basis. On average, the cost of removing the coating (depending on the type and strength of the coating used on the car) starts at €179 for the front and €459 for the entire car. In partial polishing, for example, the cost of polishing work is charged at an hourly rate of €120. Helpful guide: What to consider before installing a ceramic coating
1.3. The amount of insects/bird droppings/tree sap on the front of the car. In the summer, insects’ traces accumulate on the front of the car, which easily adhere to the paint surface. Not all of them come off even with the most effective chemicals, so they need to undergo a polishing process. The existence of burnt insects is therefore entirely individual and not a completely regular phenomenon. To prevent insects from becoming “fossils” under the transparent PPF protective film, it is important to remove them. Insect removal is charged at an hourly rate of €120, and statistically, it takes 0.7 hours (€84) to apply Full Front PPF protection film to a car. In partial polishing, the cost of insect removal polishing work is charged at an hourly rate of €120.
1.4. We recommend repairing only the largest and most visible stone chips, visible when standing at eye level in front of the car. We do not recommend repairing all small stone chips, as this would result in a “repaired” appearance. Customer special requests are taken into account, and if a customer wants every small stone chip repaired, it is done exactly as the customer wishes. Stone chip repair is not typically included in the price estimate for PPF protection film installation unless specifically agreed upon. Repair is carried out at €120/hour + possible car paint jar ~€30 (it is also possible for the customer to bring their own jar from the importer). Stone chip repair is a separate procedure from the protection film application process, and their costs are not included in each other’s costs.
2. Schedule: In order for the PPF film to meet warranty conditions and technical requirements due to its robust durability, PPF must always dry overnight, so the larger the area covered by the protective film, the more installation time + drying time it requires.
2.1. In winter, we observe 2 full drying days, and in summer, 1-2 days.
2.2. If a Full Front Kit is applied to the car, it is taken in for work on Monday morning, for example, and delivered on Wednesday morning.
2.3. For full car protection film application, the car is worked on for 5 weekdays, and the car must stand and dry for an additional 2 days. For example, taken in for work on Monday, delivered the following Monday.
2.4. If the car is brought in for installation later than the originally agreed upon date, the originally planned delivery date for the car naturally moves forward.
3. It is impossible to apply protective film to black rough parts because the tape/film does not adhere to it, not even the paint. These areas are never included in the price estimate or execution. These areas usually include lower sills, wheel arch moldings, front/rear bumper lower parts, depending on the car brands. This area is easily identifiable, it is matte black, rough plastic.
4. Before starting work, it is important that the car’s paint surface is installation dry after painting. If you are unsure about the dryness of the car’s paint surface, whether it is new or used, please verify the matter with the selling dealer/previous owner for possible fresh paintings. After painting, the car must dry for at least 4-6 weeks before the safe taping process. Usually, the delivery date for new cars is at least this 4-6 weeks after the car has come out of the oven after painting. In new cars, however, transport damage may sometimes occur during logistics, requiring painting. Specifically, these situations need to be clarified and communicated to Restyling Point.
5. Based on what we see daily in different car models, we can say that today in the automotive industry, there is a trend towards more features in the paint surface that have not been present in the automotive industry before. In other words, the quality of the paint surface seems to be changing over the decades. As a result, we may encounter more frequently cases such as:
5.1. Debris under the paint surface, as well as between the paint and clear coat. This is particularly evident under the film as “bubbles” because there is a protrusion under the film that forms a needle-point-sized air pocket around it, resembling an “air bubble.” Depending on the car manufacturer, this feature is more common for some car brands.
5.2. Panel gaps, i.e., gaps between body parts. Asymmetrical fit of body parts may affect the symmetrical installation of the PPF film, e.g., from under the headlight, which is a very common sight. In practice, for example, the film can be taken under one headlight and not the other if the light is attached to the bumper.
6. If the delivery time of a new car is delayed, we ask to be notified of this as soon as possible at Restyling Point so that we can adapt to the new schedule with changes.
General Regarding Responsibility and Warranty
Restyling Point’s values include honesty, transparency, continuous learning, and trust. Therefore, we behave responsibly towards the consequences of the installation and use the opportunity for analysis and the opportunity to learn and gain experience. In an industry that is 100% handmade, we do not deny the possibility of errors, but we strive in every possible way to avoid and minimize the occurrence of human errors in craftsmanship. Every possible error we make is documented, and the matter is never left unanalyzed or undeveloped. We inform the customer in advance of even the smallest possible risks, situations that we can predict based on the information provided by the customer before performing the work, or that we have in our possession based on experience. Due to the responsibility and respect based on Restyling’s corporate culture towards the customer, we are obliged to minimize the risks to the customer.
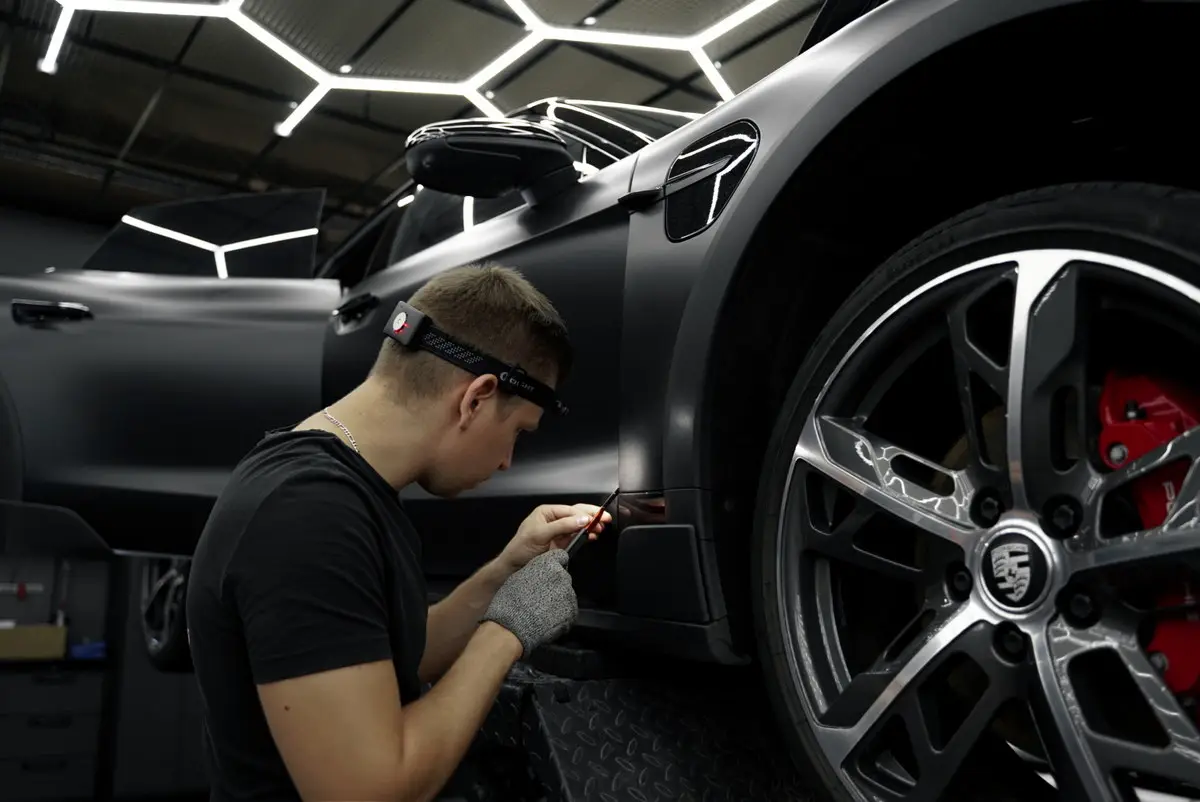
Restyling Point’s mission is to find the best possible raw materials on behalf of the customer, which are currently available in the industry, and install them in the most durable way possible on the customer’s vehicle.
Restyling Point does not chemically manufacture the products/raw materials it uses, such as tapes, coatings, films, etc. Instead, we innovatively keep our eyes open for new products, test them, and continuously search for the latest and best product technology so that our customers get the freshest, tested, and highest quality products in the automotive care industry. We do not prioritize price in the product, but rather focus on quality. It is important to us that the product/service is the latest in technology and that the customer gets the best possible value for their money.
In our industry, there are no official written global installation standards, but rather definitions based on experience/opinion that are more orally known among professionals. Regarding the installation of tapes/coatings/etc., this industry is 100% handmade craftsmanship, so there are many subjective opinions among individual professionals.
Restyling Point’s mindset regarding quality standards and implementation methods has been created by collecting and constantly monitoring the above-mentioned definitions and subjective opinions circulating in the industry, which describe the general quality standard. We filter out the above, leaving only the facts and verified aspects, and based on risk analysis, we select more opportunities for the most successful/quality installation method/product/raw material, etc. We are always open to new methods and products and approach innovations cautiously, only accepting new things entirely after testing or keeping only functional and fact-based methods for our use. We are constantly evolving.
In addition to the above operating model, we refuse to take responsibility in cases where the responsibility for the error/situation lies with another legal/private entity/organization that originally created the situation or was significantly responsible for it. We separate subjective opinions and rely only on facts.
General Information about Materials and Quality Standards
PPF, or Paint Protection Film, is an innovative film product designed to protect vehicles from daily damage. PPF film is developed to be the one that takes all the damage that would otherwise affect the paint.
PPF film is a product applied to the surface of a car/other object with the purpose of acting as a shield, fully or at least minimizing damage to the paint or the installed surface. PPF protective film cannot perform miracles if a large stone hits the car hood. The film is not eternal, nor does it endure unlimited use. Instead, the film is an ever-evolving innovative product, which today is in its most effective version and form, better, higher quality, and more durable than ever before. The product has significantly evolved over time, and based on the analysis of its development trend, we believe that there is no regression in its progress.
The film is designed to withstand and mitigate the most common stresses that the paint cannot endure and that would otherwise be visible on the paint, affecting the appearance and resale value of the object. The film is intended to suffer if the load on it reaches the limits of its protection/durability capabilities. If the film sustains significant damage, it means that the human-made product has reached its maximum limit, and it may be time to repair/replace it.
It is important to remember; if not for the film, the consequences would have been invaluable and costly on the paint. PPF, or Paint Protection Film, is, as its name suggests, a paint protection film. It is like a shield in front of the installation object, day and night, 24/7, in heat and cold, even when improper maintenance is performed on the car.
“Shoes wear out when we walk. PPF film wears out just the same.”
In this case, the film should specifically be the protective shield that, based on its limited capabilities, is exposed to physical and chemical stress, giving its best effort so that the customer’s protected installation remains untouched. The film is not an endless product, although it is designed with extremely high quality and installed according to high standards for the most rigorous use.
PPF film has its limitations, which are not present, for example, with traditional vinyl film (differences can be read about here). Therefore, at Restyling Point, we do not settle for how this material is installed globally. Because we see certain shortcomings in it. We have created our own quality standards, which every installer at Restyling Point adheres to. We refine these standards daily.
We try to manipulate PPF film with all possible safe means to often go as far as it is not normally taken internationally with common installation standards. We carry out a significant amount of extra work to minimize the customer’s risks. All of this is for one and only sacred motive; we make efforts for the benefit of our customers for the most durable installation of the product, and we are willing to sometimes go into the so-called gray area regarding the film’s durability, always considering our customers’ interests (this expression refers only to how far we hide the film).
In theory, Restyling Point could very well adopt an identical standard to that of the majority of installation shops globally, but then Restyling Point’s customers would not get the most durably installed product, precisely when the car undergoes unusually heavy stress.
Restyling’s mindset is to eliminate even the smallest risk situations for our customers, even in situations where the car is used or washed incorrectly, whether accidentally or intentionally. As a concrete example, there are areas such as edges, which are commonly left flat around the world. The reason for this is to simplify the installation, reducing the installation cost and the mindset of “doing just fine” or adhering to the so-called “80/20 rule”.
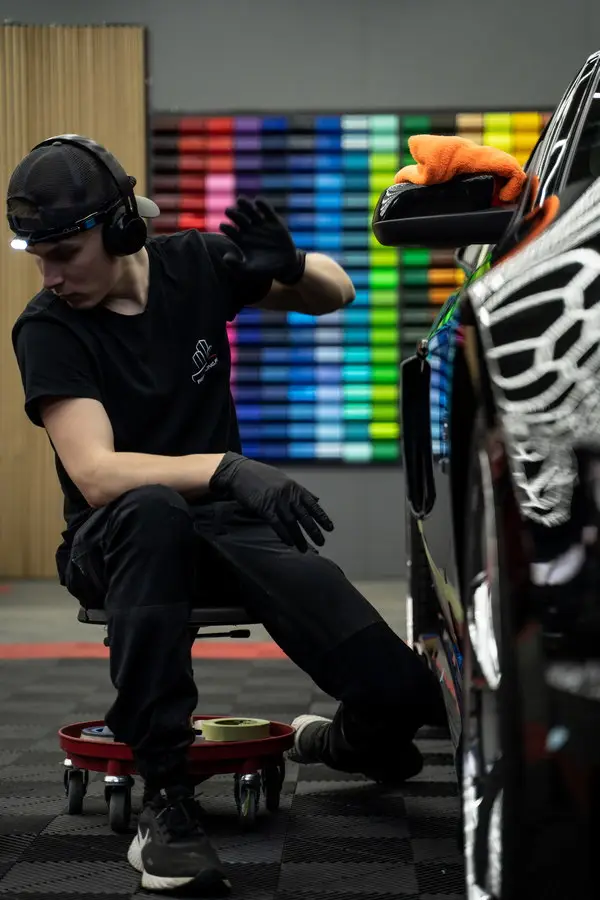
With experience, we understand the various ways in which cars can be washed in car washes. Restyling Point’s mindset looks at things from the customer’s perspective, taking into account their life situations and human circumstances. We understand that one of the limited resources is time, so there may not always be time or resources to hand wash a car due to a hectic routine and the priority of life’s essentials; it is simply easier to wash a car in a machine. Even for these reasons (although machine washes are not covered by Restyling Point’s warranty), we still adhere to and develop our quality standards, where we minimize customer risks even when they use their car in a machine wash.
Statistically, ~70% of our customers, after having PPF service done at Restyling, admit afterwards that they regularly use machine washes for their cars. And these customers do not report feedback on the film peeling off, precisely because we have already minimized their risks in advance; about 90% of the installed film edges are tucked away and simply do not undergo pressure washer stress.
Visual aspect is also crucial in the PPF film installation process. We believe that the installation must be as inconspicuous as possible.
There are approximately 50 linear meters of edges in a car. With Restyling Point’s internal written quality standard, for example, in the case of a full car PPF protection wrap, over 90% of the car’s edges are hidden and protected from stress. This is a significant benefit considering the maximum durability of the protective film, the protection of the car, and the most inconspicuous installation result possible.
In addition to its excellent resistance to stone chips and scratches, the PPF protective film has limitations that it cannot exceed. These limitations refer to whether, for example, side mirrors can be made without seams from a single piece, or bumpers and other round-shaped parts can be made without seams or stretching marks from a single piece. This is not at all about the level of skill or its absence. It’s only about the material’s capabilities. The material has its own physical technical limitations on how it can be installed on round shapes. Therefore, the existence of seams and tape joints, for example, in bumpers, mirrors, round trunks, front doors with a mirror in the middle of the flat surface; the existence of seams and joints is mandatory for the PPF to withstand use and protect the installation object as well as possible. Seams should never overlap, (unless it is matte PPF and the area next to the tire requires extra protection and sometimes exceptional solutions due to exceptional wear). In round and challenging surfaces, there is also a possibility of minor stretching marks. However, stretching marks must be minimized, and if in order to maintain the most durable product, the protective wrapping of the body part should be done in one piece, stretching marks can be a compromise at this point.
The seams of the PPF film are always butt seams, with a maximum allowable distance of 2-3 mm between the edges of the films. Seams wider than 3 mm and uncoated areas are not acceptable according to Restyling Point’s standards.
We use the most modern installation method, which is not the easiest or the cheapest, but it guarantees the highest quality and fastest result, as well as minimizing risks to the customer’s property. With a paid license program, we customize each piece according to Restyling Point’s own standards to achieve the highest quality and most durable result for the customer’s vehicle through installation.
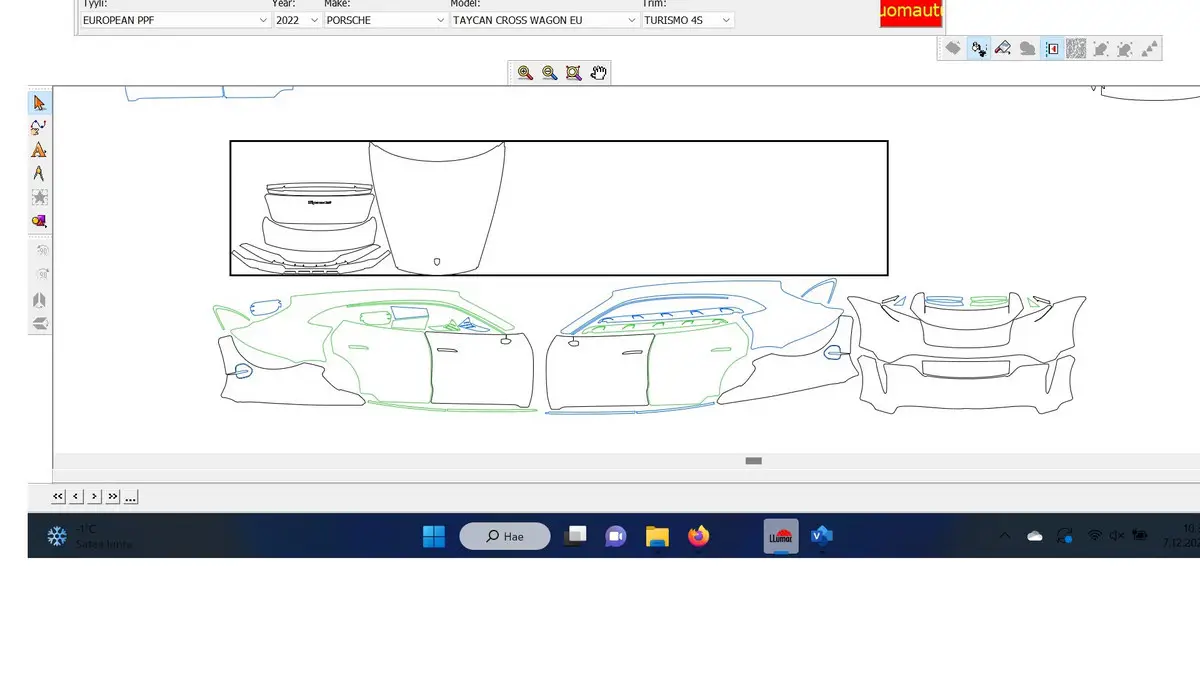
These things are done out of love for the profession and the belief that our customers are invaluable to us. Our mission is to serve our customers and advance our industry so that its reputation and popularity grow, as this results in a win-win situation from the customer’s perspective as well.
If we were driven solely by money, we wouldn’t have quality standards, and the installed products wouldn’t stay in place. The reputation of the industry and the product would suffer. And the customer would receive poor value for their money.
In our warranty terms, we continuously update important information for the customer in response to new situations so that the customer knows what to expect and what to prepare for. Our intention is to be completely transparent and provide clear information for customer anticipation.
PPF film cannot adhere to sharp protrusions or creases. Examples of situations:
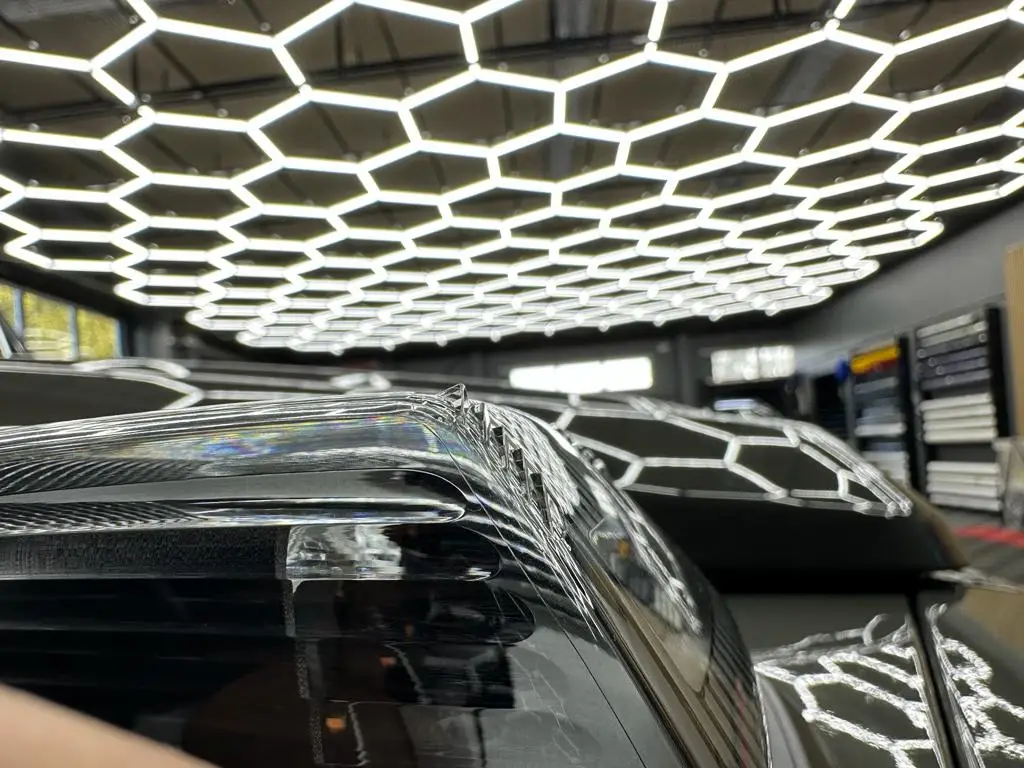
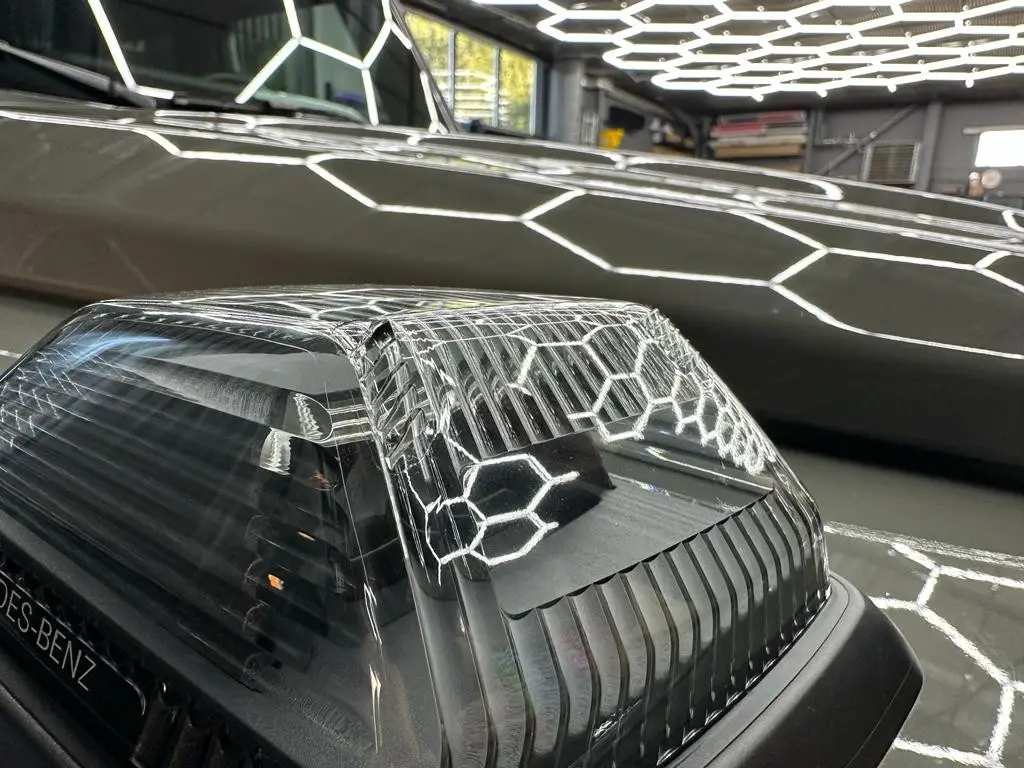
In the case of the Mercedes-Benz G Wagon, where there’s a sharp protrusion in the corner of the front fog light, it must be left uncovered by the film because the film cannot adhere to it. Another option is to leave it unopened, creating a large air pocket around it, if that’s acceptable to the customer.
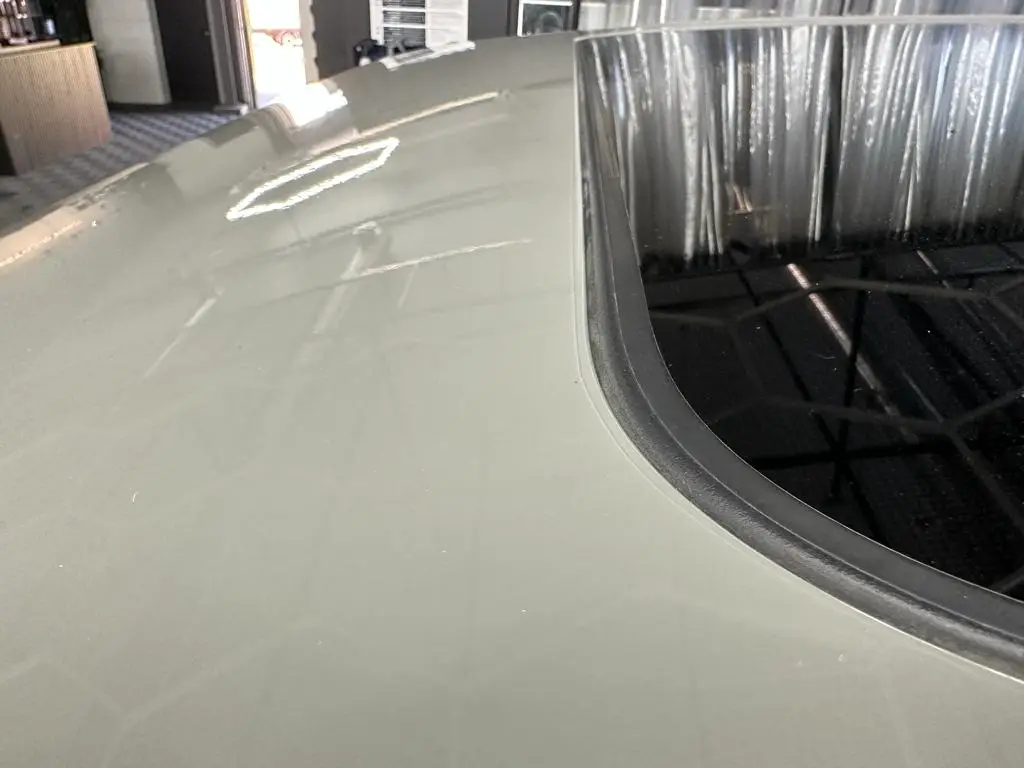
In tight seals, the film cannot always be tucked under the seal. Some seals may cause excessive rubbing against the film, affecting the adhesion of that particular film edge.
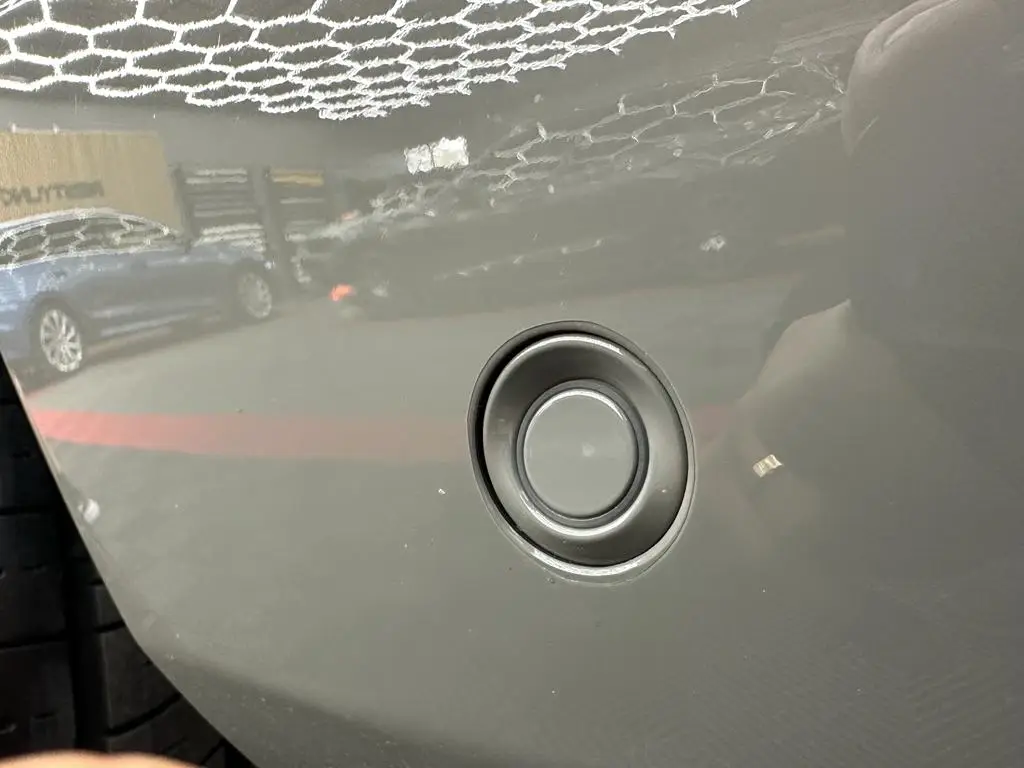
Deeper parking sensors are always cut open unless the customer specifically requests not to. Otherwise, leaving them uncut would result in a large air pocket, which could affect the functionality of the parking sensor. There is a risk of damaging the edge of the film around the cut-open parking sensor if incorrect washing methods are used or due to natural wear and tear during the vehicle’s use.
During the installation of the PPF protective film, a few dust particles may occasionally get trapped underneath, which is a normal phenomenon. Restyling Point is responsible for minimizing the ingress of dust particles under the film in every possible way, but due to the human craftsmanship involved, some particles may occasionally remain under the film.
If a used vehicle is fitted with protective tape, any existing stone chips and scratches will remain visible. The finest washing scratches are completely concealed by the PPF film, but deep scratches are not.
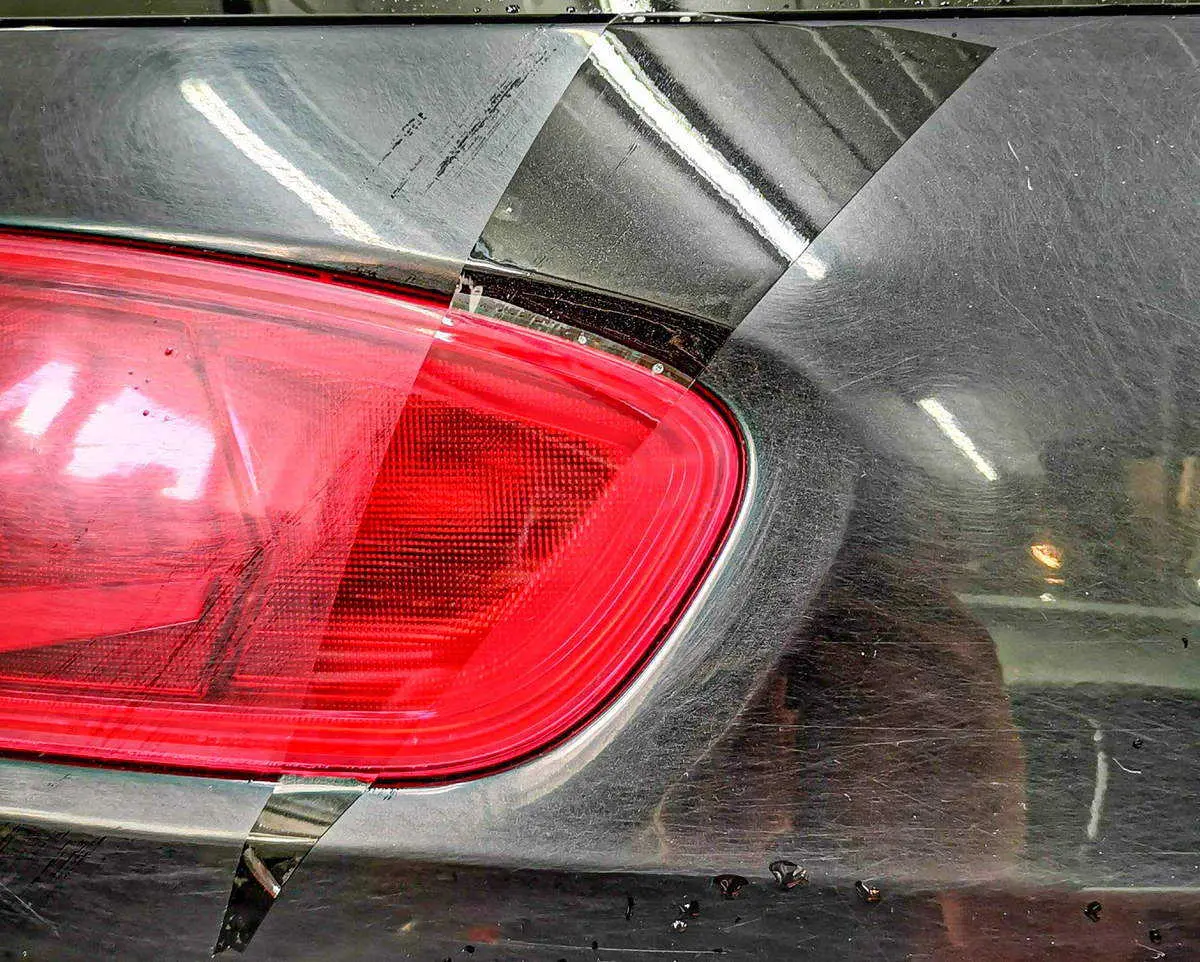
Lifetime AfterCare Maintenance Program
In addition to traditional warranty terms, we have created a free maintenance program for our PPF customers. For years, we have implemented a lifetime AfterCare maintenance program for our PPF customers at no cost. This is an individual product maintenance procedure. This maintenance procedure only applies to film detachment caused by natural product wear or intentional or unintentional use.
In practice, this means that if a customer washes their car incorrectly with a pressure washer and causes damage to the film, we aesthetically remove the visibly detached piece. The repair procedure should take a maximum of 5-10 minutes, and it does not include the installation/gluing process of a patch piece or any other repair. Or if the PPF protective films installed at the level of the tires and adjacent areas detach or change appearance to look unsightly, we will cut out the areas requested by the customer.
The purpose of the AfterCare maintenance program is to provide customers with ease of use for PPF film because we understand the facts about the product and inform customers about the real usage possibilities of the PPF product, thereby ensuring the presentable appearance and condition of the installed PPF film.
In AfterCare maintenance repairs, the customer does not pay for cutting out the damaged area. The customer can come for the repair without making an appointment, but in that case, they may have to wait depending on the installation situation. It is best to arrange the AfterCare maintenance repair time with the shop in advance.
Restyling Point’s PPF AfterCare maintenance program applies for the lifetime of the customer to the car for which they originally purchased PPF installation from Restyling.
The AfterCare maintenance program cannot be transferred with a change of ownership. After a change of ownership of the car, the normal warranty for the product/service applies.
We reserve the right to make changes.
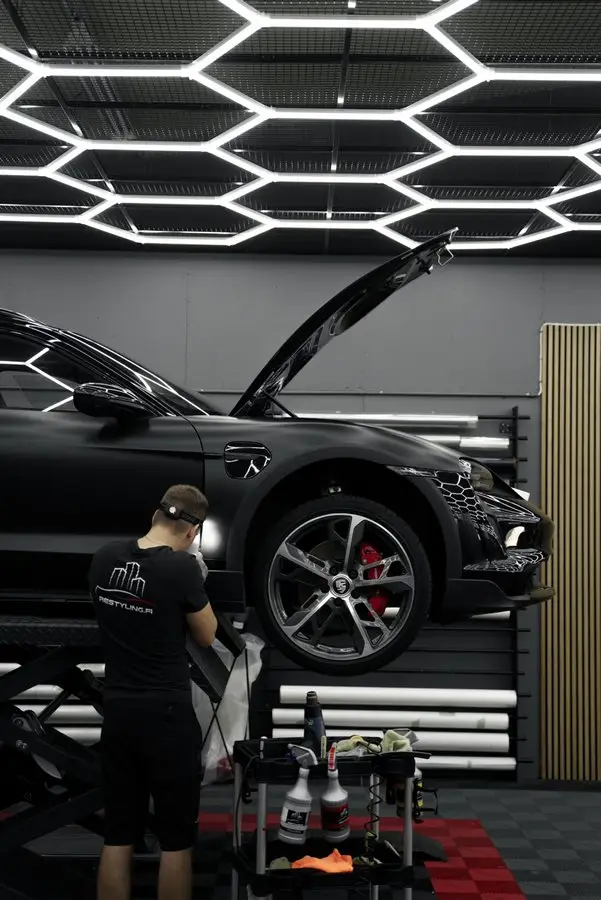
Cancellation Terms and Payment
1. Cancellation Terms
1.1. When it comes to smaller PPF services, such as individual body part wrapping (e.g., cargo protection, interior thresholds, headlights, or similar small tasks), you can reschedule or cancel your appointment free of charge if you do so at least 48 hours before the scheduled time. Changing or canceling appointments can be done in three different ways:
-
- by calling +358 445050624
- by sending an email to [email protected]
- by sending a message via WhatsApp or text message
1.2. Reserved appointments must be canceled at least 48 hours before the start of the appointment. For cancellations made later or for entirely missed appointments, we reserve the right to charge the full price of the reserved service.
2. Advance Payment
2.1. A 50% advance payment for the entire car PPF wrapping is required when scheduling the project.
2.2. For PPF wrapping, we pre-cut the templates with licensed software and prepare them for installation based on the car model/additional model or photos provided by the customer if they do not yet own the car. We follow a cost-effective and preparatory approach to ensure that customers’ schedules are maintained and service prices are reasonable. Therefore, individually handcrafted films for vehicles cannot be installed on other brands or models.
2.3. If a customer cancels the order after confirming the order confirmation, and we have already begun irreversible pre-preparation procedures, Restyling Point Oy reserves the right to charge the costs incurred from material procurement and modification, and the customer will receive the ordered material without refund. Costs typically include material costs + shipping costs, template modifications, film cutting, and finishing work. In some cases, the material is ordered in advance to a specific size and cannot be returned to the importer. Due to long logistics delays nowadays, the material must always be ordered in advance.
3. Payment is made after the car is delivered to the customer ready for use. Payment methods include credit card and bank transfer. Invoicing is available to customers with a history at Restyling Point. We do not offer installment payments.
After PPF Installation
After receiving the car ready, it is important to familiarize yourself with the washing instructions and general tips and take into account the warranty terms.
Do you want the work to be done responsibly, on schedule, and with the best value for your money? Ask for a quote from Restyling Point professionals, who do this with quality standards, values, and love.
WhatsApp: +358445050624
Phone: +358445050624
Email: [email protected]
Restyling Point Oy – Leader in wrapping and protection treatments in the Nordics